Технические требования к обработке деталей машин
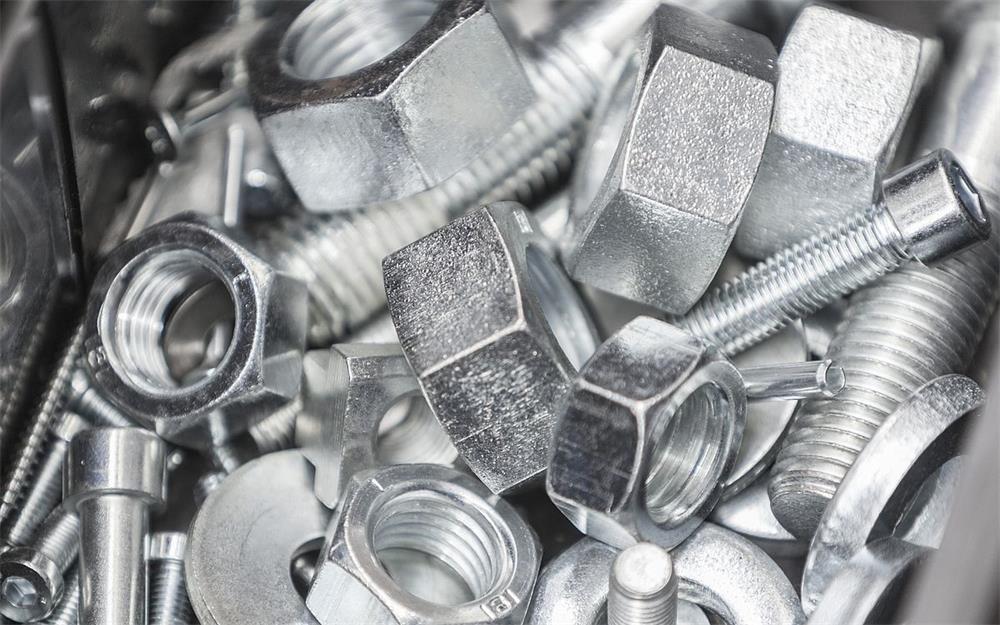
После того, как проектирование деталей машин завершено, необходимо провести ряд обработок, чтобы обеспечить точность обработки деталей. Затем в конкретном процессе обработки мы должны строго соблюдать следующие технические требования для обработки деталей машин .
Обработка поверхности деталей
1. На обрабатываемой поверхности деталей не должно быть царапин, потертостей и других дефектов, повреждающих поверхность деталей.
2. На поверхности обрабатываемой резьбы не должно быть таких дефектов, как почернение кожи, неровности, случайные пряжки и заусенцы. Перед покраской с поверхности всех стальных деталей, подлежащих окраске, необходимо удалить ржавчину, оксидную окалину, жир, пыль, почву, соль и грязь.
3. Перед удалением ржавчины используйте органические растворители, щелочь, эмульгатор, пар и т. д. для удаления жира и грязи с поверхности стальных деталей.
4. Интервал времени между поверхностью, подлежащей покрытию дробеструйной очисткой или ручным удалением ржавчины, и нанесением грунтовочного покрытия не должен превышать 6 часов.
5. Поверхности заклепочных частей, соприкасающиеся друг с другом, перед соединением должны быть окрашены антикоррозийной краской толщиной 30-40 мкм. Края внахлест должны быть покрыты краской, шпаклевкой или клеем. Грунтовка, поврежденная обработкой или сваркой, должна быть перекрашена.
Термическая обработка деталей
1. После закалки и отпуска HRC50~55.
2. Среднеуглеродистая сталь: детали 45 или 40Cr подвергаются высокочастотной закалке, отпуску при 350~370℃, HRC40~45.
3. Глубина науглероживания составляет 0,3 мм.
4. Проведите высокотемпературную обработку старением.
Технические требования после отделки
1. Готовые детали не должны размещаться непосредственно на земле при размещении, и должны быть приняты необходимые меры поддержки и защиты.
2. На обработанной поверхности не должно быть дефектов, таких как ржавчина, неровности и царапины, которые влияют на производительность, срок службы или внешний вид.
3. Поверхность, обработанная прокаткой, не должна отслаиваться после прокатки.
4. На поверхности деталей после термической обработки в конечном процессе не должно быть оксидной окалины. Обработанные сопрягаемые поверхности и поверхности зубьев не должны подвергаться отжигу.
Герметизация деталей
1. Перед сборкой все уплотнения необходимо пропитать маслом.
2. Строго проверьте и удалите острые углы, заусенцы и посторонние предметы, оставшиеся при обработке деталей перед сборкой. Убедитесь, что уплотнение не поцарапано при его установке.
3. После приклеивания удалите излишки вытекающего клея.
Технические требования к снаряжению
1. После сборки шестерни пятна контакта и люфт поверхности зуба должны соответствовать требованиям GB10095 и GB11365.
2. Контрольный торец шестерни (червячной передачи) и буртик вала (или торец позиционирующей втулки) должны совпадать и не могут быть проверены щупом 0,05 мм. И должен обеспечить требования к вертикальности опорного торца шестерни и оси.
3. Поверхность соединения редуктора и крышки должна быть в хорошем контакте.
Технические требования к подшипникам
1. При сборке подшипников качения допускается использовать масляный нагрев для горячей заправки, при этом температура масла не должна превышать 100°С.
2. Полукруглые отверстия наружного кольца подшипника, а также открытое гнездо подшипника и крышка подшипника не должны заедать.
3. Наружное кольцо подшипника должно плотно прилегать к полукруглому отверстию открытого посадочного места подшипника и крышки подшипника. При проверке окраской она должна быть симметричной с посадочным местом подшипника под углом 120° к средней линии, а с крышкой подшипника в пределах 90° симметричной средней линии. Даже контакт. При проверке щупом в указанном выше диапазоне щуп 0,03 мм не должен вставляться на 1/3 ширины наружного кольца.
4. После сборки внешнее кольцо подшипника должно равномерно соприкасаться с торцом крышки подшипника установочного конца.
5. После того, как подшипник качения установлен, его следует гибко и плавно вращать вручную.
6. Поверхности соединения верхней и нижней подшипниковых втулок должны плотно прилегать и не могут быть проверены щупом 0,05 мм.
7. При фиксации втулки подшипника с помощью установочных штифтов просверлите распорный и распределительный штифты, следя за тем, чтобы открывающая и закрывающая поверхности и торец поверхности втулки и торец соответствующего отверстия подшипника находились заподлицо друг с другом. Не ослабляйте штифт после вбивания.
8. Корпус подшипника сферического подшипника и гнездо подшипника должны находиться в равномерном контакте, и контакт не должен быть менее 70% при проверке методом окраски.
9. Футеровка подшипника из сплава не может использоваться, когда поверхность желтая, и зародышеобразование не допускается в пределах указанного угла контакта, а площадь зародышеобразования вне угла контакта не должна превышать 10% от общей площади. бесконтактная зона.
Технические требования к винтам, болтам и гайкам
1. При затягивании винтов, болтов и гаек категорически запрещается ударять или использовать неподходящие отвертки и гаечные ключи. Пазы для винтов, гайки и винты, а также головки болтов не должны быть повреждены после затяжки.
2. Крепеж с указанным моментом затяжки необходимо затягивать динамометрическим ключом.
3. При креплении одной и той же детали несколькими винтами (болтами) каждый винт (болт) необходимо затягивать крест-накрест, симметрично, постепенно и равномерно.
4. Плоская шпонка и две стороны шпоночного паза на валу должны находиться в равномерном контакте, и между сопрягаемыми поверхностями не должно быть зазора.
Технические требования к ремонтной сварке
1. Дефекты должны быть полностью устранены перед ремонтной сваркой, а поверхность разделки должна быть отремонтирована ровно и без острых углов.
2. В зависимости от дефектов стальных отливок, дефекты в зоне ремонтной сварки могут быть удалены лопатой, шлифовкой, строжкой угольной дугой, газовой резкой или механической обработкой.
3. Грязь, такую как липкий песок, масло, вода, ржавчина и т. д. в пределах 20 мм вокруг области ремонтной сварки и канавки, необходимо тщательно очистить.
4. В течение всего процесса ремонтной сварки температура зоны предварительного нагрева стальных отливок должна быть не ниже 350°С.
5. Если позволяют условия, сваривайте как можно больше в горизонтальном положении.
6. При ремонтной сварке сварочный стержень не должен делать чрезмерного бокового раскачивания.
7. При наплавке на поверхность стальных отливок нахлест между валиками должен быть не менее 1/3 ширины валика.
Технические требования к отливкам
1. Зона допуска отливки симметрична базовой размерной конфигурации черновой отливки.
2. На поверхности отливки не допускаются холодные перегородки, трещины, усадочные раковины, сквозные дефекты и серьезные неполные дефекты (подлив, механические повреждения и т.п.).
3. Отливки должны быть зачищены без заусенцев и заусенцев. Разливочные стояки по необработанным показаниям должны быть очищены и заподлицо с поверхностью отливок.
4. Литейные знаки и отметки на необработанной поверхности отливки должны быть четкими и узнаваемыми, а положение и шрифт соответствовать требованиям чертежа.
5. Шероховатость необработанной поверхности отливки, отливки в песчаные формы R, не более 50 мкм.
6. Отливки должны быть очищены от стояков заливки, шпор и т.п. Остатки стояка заливки на необработанной поверхности должны быть выровнены и отшлифованы до требований к качеству поверхности.
7. Формовочная смесь, стержневой песок и стержневая кость на отливке должны быть очищены.
8. Отливка имеет наклонные части, при этом зона допуска на размеры должна располагаться симметрично вдоль наклонной плоскости.
9. Формовочный песок, стержневой песок, стержневую кость, мясистый, липкий песок и т. д. на отливках должны быть сглажены и очищены.
10. Правильный или неправильный тип, отклонение отливки бобышки и т. д. должны быть исправлены для достижения плавного перехода и обеспечения качества внешнего вида.
11. Морщины на необработанной поверхности отливки должны иметь глубину менее 2 мм и расстояние между ними более 100 мм.
12. Необработанная поверхность отливок изделий машинного производства должна быть подвергнута дробеструйной или валковой обработке для соответствия требованиям уровня чистоты Sa2 1/2.
13. Отливки должны быть обработаны водоотталкивающими средствами.
14. Поверхность отливки должна быть гладкой, а литник, заусенец, липкий песок и т.п. должны быть удалены.
15. Не допускается наличие в отливках дефектов литья в виде холодных перегородок, трещин, отверстий и т.п., неблагоприятных для эксплуатации.
Технические требования к поковкам
1. Форсунки и стояки каждого стального слитка должны быть удалены достаточно, чтобы поковки не имели усадки и серьезного прогиба.
2. Поковки следует выковывать на кузнечном прессе достаточной производительности, чтобы поковки были полностью прокованы.
3. Не допускается наличие на поковках видимых трещин, складок и других дефектов внешнего вида, влияющих на эксплуатацию. Местные дефекты можно удалить, но глубина зачистки не должна превышать 75 % припуска на обработку. Дефекты на необработанной поверхности поковки должны быть очищены и плавно переходить.
4. В поковках не допускаются белые пятна, внутренние трещины и остаточные усадочные отверстия.
Zhongken предлагает различные типы и спецификации деталей машин, которые могут удовлетворить специфические потребности различных приложений и имеют длительный срок службы. Если вам это нужно, вы можете напрямую искать сопутствующие товары на нашем веб-сайте и связаться с нами.
Как производитель запчастей , мы всегда стремимся предоставлять клиентам качественные продукты и услуги. У нас есть специализированное производственное оборудование и создана полная система контроля качества для строгого контроля качества нашей продукции. В то же время наша полная команда менеджеров может предоставить продуманное комплексное обслуживание и разработать эффективные решения в соответствии с разнообразными потребностями клиентов. Если вы заинтересованы в наших частях машин, пожалуйста, свяжитесь с нами немедленно!